Download a pdf version of this data sheet for printing and future reference. (right click and select save to disk) |
303 Austenitic Stainless Steel Bar |
303 is a free machining chromium-nickel austenitic stainless steel with good strength and good corrosion resistance, as supplied in the annealed condition with a typical brinell hardness of 190.
Characterised by excellent machinablity and non galling properties due to its higher sulphur content, which has the effect of lowering slightly its corrosion resistance. It is however, fairly resistant to general atmospheric corrosion, general foodstuffs, sterilizing solutions, dyestuffs, most organic chemicals, plus some inorganic chemicals. But has very limited resistance to acids.
303 cannot be hardened by thermal treatment, but strength and hardness can be increased substantially by cold working, with susequent reduction in ductility.
It is used primarily for production runs involving extensive machining, or complex parts requiring excellent machinability.
Typical uses are:
Architectural Components, Food Processing Equipment, Dairy Equipment, Dying Industry, Hardware and Kitchenware manufacturing and allied industries. Commonly used to manufacture Bolts and Nuts, Bushes, Gears, Shafts, Valve Bodies and Fittings etc..
Material non magnetic in the annealed condition, but can become mildly magnetic following heavy cold working. Annealing is required to rectify if necessary.
|
Colour Code
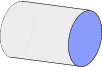 |
Pale Blue
(Bar end) |
|
Stocked Sizes |
6 mm to 150 mm diameter. |
Bar Finish |
Peeled, Cold Drawn, Turned and Polished, and Centreless Ground. |
Related Specifications |
|
Australia |
AS 2837-1986-303 |
Germany |
W.Nr 1.4305 X10CrNiS 18 9 |
Great Britain |
BS970 Part3 1991 303S31
BS970 1955 EN58M |
Japan |
JIS G4303 SuS 303 |
USA |
ASTM A582/582M-95b 303
SAE 30303 AISI 303
UNS S30300 |
Chemical Composition |
Min. % |
Max. % |
*Molybdenum optional addition. |
Carbon |
0 |
0.15 |
Silicon |
0 |
1.00 |
Manganese |
0 |
2.00 |
Nickel |
8.00 |
10.00 |
Chromium |
17.00 |
19.00 |
*Molybdenum |
0 |
1.00 |
Phosphorous |
0 |
0.06 |
Sulphur |
0.15 |
0.35 |
Mechanical Property Requirements - Annealed to ASTM A582/A582M-95b 303 |
Condition |
Hardness |
Annealed |
HB 262 Max. |
|
Typical Mechanical Properties At Room Temperature - Annealed |
|
Finish |
Tensile
Strength
Mpa |
Yield
Strength
Mpa |
Elongation
in 50 mm
% |
Impact
Charpy V
J |
Hardness |
|
HB |
Rc |
Cold Drawn |
720 |
510 |
36 |
|
220 |
20 |
Other |
600 |
240 |
55 |
120 |
165 |
|
Elevated Temperature Properties |
303 displays good oxidation resistance in continuous service up to 870 oC and in intermittent service up to 760 oC.
Continuous service however, between 430 oC and 850 oC is not recommended, nor is slow cooling through this range due to the problem of intergranular corrosion.
N.B. High temperature use is therefore not generally recommended.
|
Cold Bending |
303 has very limited cold bending properties and it is not generally recommended.
|
Hot Bending |
Hot bending should be performed at 950 oC - 1100 oC, followed by annealing to restore optimum corrosion resistance.
|
Corrosion Resistance - All Corrosion Types |
303 due to its higher sulphur content has lower resistance to all corrosion types than 304, and indeed all of the 300 series austenitic stainless steels.
Its selection therefore is generally based upon its excellent machinability, coupled with its lower corrosion resistance.
N.B. It is most important that oxygen is always allowed to circulate freely on all stainless steel surfaces to ensure that a chrome oxide film is always present to protect it. If this is not the case, rusting will occur as with other types of non stainless steel.
For optimum corrosive resistance surfaces must be free of scale and foreign particles. Finished parts should be passivated.
|
Forging |
Heat uniformly to 1150 oC - 1200 oC, hold until temperature is uniform throughout the section.
Do not forge below 900 oC
Finished forgings should be air cooled.
Finally forgings will require to be annealed in order to obtain optimum corrosion resistance.
N.B. Severe upset forging of this grade is not recommended.
|
Heat Treatment |
Annealing |
Heat to 1050 oC - 1100 oC, hold until temperature is uniform throughout the section. *Soak as required. Quench in water to obtain optimum corrosion resistance.
*Actual soaking time should be long enough to ensure that the part is heated thoroughly throughout its section to the required temperature, 30 minutes per 25 mm of section may be used as a guide.
Please consult your heat treater for best results.
|
Machining |
303 was developed as a free machining grade, and has by far the best machinability of all the 300 series austenitic stainless steels, and indeed has better machinability than most of the 400 series martensitic stainless steels with the exception of the free machining grades. It has a typical machinability rating of about 75% - 80% of free machining (S1214) mild steel.
It has however, as with all austenitic stainless grades, a high work hardening rate and cutting or drilling tools etc. must be kept sharp at all times and not cause unecessary work hardening of the surface.
All machining should be carried out as per machine maunfacturers recommendations for suitable tool type, feeds and speeds.
|
Welding |
303 is not generally recommended for welding due to its high sulphur content which can cause hot cracking.
However if unavoidable, the following procedures may be taken as a guide.
|
Welding Procedure |
Welding electrodes or rods should be 308 or *similar depending upon application.
No pre heat or post heat is generally required.
Post weld annealing will be required to restore corrosion resistance.
*Please consult your welding consumables supplier.
|
Interlloy believes the information provided is accurate and reliable. However no warranty of accuracy, completeness or reliability is given, nor will any responsibility be taken for errors or omissions. |
|